Entwicklung von RIM-Werkzeugen für Highend-Wassersportgerät
17.11.2019 – Formenbau / Werkzeugbau
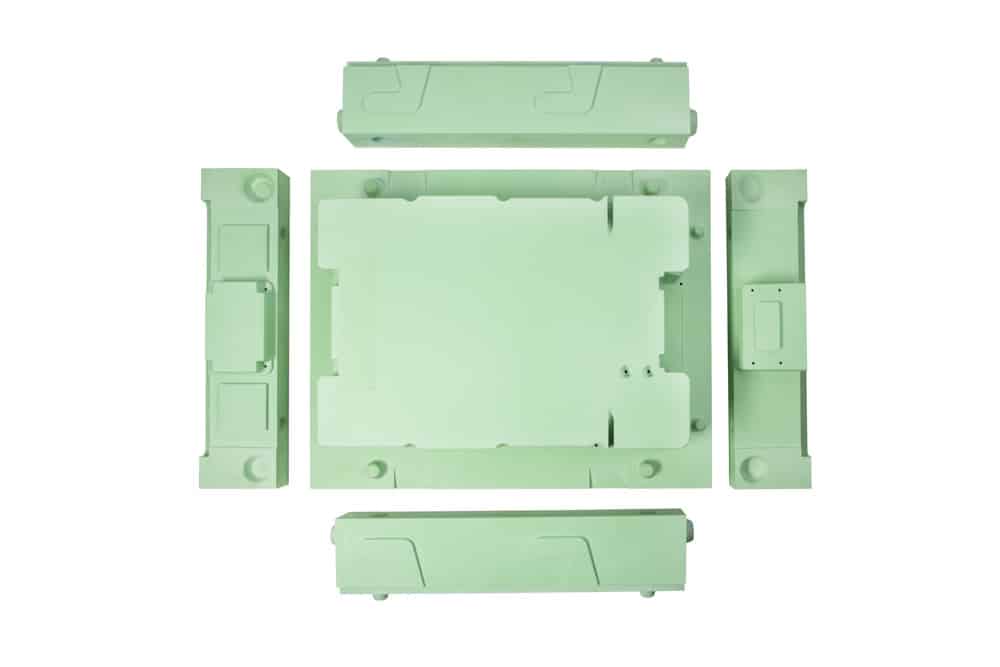
Hohen Anforderungen mit bewährtem Know-how begegnen: mit der Fertigung anspruchsvoller RIM-Werkzeuge entstehen bei HICONFORM die Formen für Bauteile eines elektrischen Wassersportgerätes.
- Umsetzung: 2019
- Projektlaufzeit: 4 Kalenderwochen
- Ansprechpartner / Projektverantwortliche:
Mike Hermsdorf, Veit Harand
01 – Kundendatenaufbereitung
02 – Werkzeugkonstruktion
03 – Abstimmung der Werkzeugauslegung mit Kunden nach Injektionssimulation
04 – finale Festlegung des Werkzeuges und Planung der Fertigung
05 – Fertigung des Werkzeuges
06 – Oberflächenfinish
In geheimer Mission und mit hohen Anforderungen
Nicht immer können wir detailliert über die Projekte sprechen, welche wir umsetzen. Oftmals stehen dahinter innovative Produkte, laufende Patentverfahren oder einzigartige Formen, welche nicht gezeigt werden dürfen. So auch bei diesem Projekt, bei dem wir für die Fertigung zweier RIM-Werkzeuge mit kurzer Laufzeit aus Kunststoffblockmaterial beauftragt wurden.
Die Formen bildeten die Basis für die Herstellung von Batteriekästen für ein elektrisches Wassersportgerät, welches im Luxussegment zu Hause ist. Für die wertige Anmutung der Batteriekästen, bestehend aus einem Boden, vier Seitenwänden und einem Deckel, war es essentiell, eine makellose Oberfläche und die filigranen Konturen zu realisieren.
Reaction Injection Moulding (RIM) als Urformverfahren für die Herstellung von Kunststoffformteilen
Reaction Injection Moulding (RIM) bezeichnet ein Formverfahren zur Herstellung von Kunststoffformteilen. In diesem Prozess werden zwei oder mehrere Komponenten bzw. reaktive Flüssigkeiten vermischt. Diese Vermischung passiert unter Hochdruck. Unmittelbar danach wird die Masse in das Formwerkzeug gespritzt. Die Aushärtung der Flüssigkeiten findet im Formwerkzeug statt – das fertige Formteil aus Kunststoff entsteht.
Mit RIM lassen sich sehr gut kleine Serien abbilden, dabei ist es ein deutlich preiswerteres Verfahren, als ein Metallwerkzeug zu fertigen.
Lösungen auch bei komplizierten Geometrien
Das Besondere bei diesen Formen waren die sehr feinen Konturen der Fertigteile, welche zu 100% am Werkzeug ausgeführt sein sollten. Als Werkzeugbauer haben wir natürlich das Know-how, auch bei komplexen Geometrien passgenaue Lösungen zu finden. In diesem Fall konnten wir durch Einsätze im Werkzeug die Realisierung feiner oder abstrakter Konturen bedingen.
„Wir können unser Know-how vielseitig anwenden und sind immer bereit, neue Wege in der Fertigung zu gehen. Wenn ein Auftraggeber mit Anforderungen kommt, die wir noch nicht umgesetzt haben, finden wir schnell Wege zur Umsetzung.
Kurzum: stimmt das gegenseitige Vertrauen, ist bei uns eigentlich alles möglich.“
Mike Hermsdorf, HICONFORM
Unser Know-how für Zukunftstechnologien
Durch die rasante Entwicklung der Technologie entstehen teils immer komplexere Formen, welche realisiert werden müssen. Zugleich werden in der Produktion bewährte Materialien durch neue Werkstoffe ersetzt, um beispielsweise Gewicht oder den Materialeinsatz zu reduzieren. Abdeckungen für Batterie- und Antriebskomponenten, ergonomische Bauteile – besonders in technologiegetriebenen Branchen wie Mobilität oder Energieversorgung können wir als Systemlieferant ein wirtschaftlicher Partner sein.